Focusing on long-term materials management and optimizing capital planning can shore up your shortage mitigation plan.
2018 and 2020 showed us that electronic component shortage is turning into a continuous issue for the supply chain. Natural disasters, industrial disasters, global politics: the challenges in the electronic component supply chain abound even in 2021.
First pushed into the spotlight with tariffs imposed by the Trump administration in 2018, politics have emerged as a major factor in market volatility for electronic components. The limited number of integrated circuit “IC” manufacturers created even more tension in the supply chain throughout the challenges of 2020. In such an environment, the one-off strategy of sourcing components in shortage won’t stand. To be successful, it’s more important than ever to embrace a shortage mitigation plan in the long term.
Shortage mitigation planning: It should be the new normal
Short term, a string of disasters has affected the semiconductor supply chain, dialing up pressure on an already strained market. The volatility of the 2020 market hit the automotive industry particularly hard. What appeared in 2020 as a short-term problem continues to play out well into 2021.
IHS Markit reported that in the first quarter nearly 1.3 million vehicles are delayed. Factors behind the delay include a natural disaster in Texas and a fire in Japan that shuttered semiconductor facilities. Both deepened existing shortage conditions. While semiconductor production supply chains sort themselves out through diversification or expansion, delays impacting your production lines present immediate concerns.
The current pressure on the automotive industry might resolve in 2021, but the undercurrent of supply chain instability that affects all sectors will likely persist. The widespread impact that we are seeing requires a comprehensive shortage mitigation plan. Action now can mitigate the impact of future shortages while upholding your quality standards.
Materials management: Focus on the long view
Materials management in the traditional sense is obsolete. With technology developments constantly pushing new components to the forefront, the need for specialized storage has broadened beyond just long-term, high-reliability components storage. The current landscape of ongoing electronic components shortages demands more cost-effective, specialized storage options to relieve pressure on manufacturers. In-house storage often creates economic inefficiencies and risks involving inadequate security or training, potentially exposing electronic components to damaging environmental conditions and ESD.
The ideal materials management solution pairs secure storage with cost savings. Bonded storage offers options for long-term purchasing security. Storing components securely in an ESD-approved warehouse equipped with safety measures protects sensitive components and provides a layer of stability. By outsourcing electronic components storage to a specialized partner, your sensitive electronic components are kept in a secure manner that allows you to meet your production schedule – and, perhaps surprisingly, this strategy can offer cost savings, if you work with the right provider.
Optimize long-term capital planning for shortage mitigation
Industry expert advice on how to beat the current shortage crisis abounds. Looking backward, HBR suggests investigating where cost reduction was prioritized over risk management in the previous year. Gartner advises resiliency balanced with cost containment for long-term supply chain optimization. An IHS Markit expert offers the following assessment for the automotive vertical:
“It will get worse before it gets better. Short term all that can be done is juggling priorities in the foundries to make more automotive MCUs instead of products for other markets. Longer term, the automotive industry needs to make supply assurance as high a priority as cost savings to incentivize the supply chain to be more diverse. Moving to more advanced process nodes makes the industry even more susceptible to a limited number of foundry options.”
Our take is that balancing supply and costs in shortage really comes back to having access to a qualified vendor base plus secured long-term storage. If you have access to established relationships with OEMs, EMS and OCMs, you’ll have more resources to draw from to build smart capital investments. These relationships are further supported with transparent, structured communications. When shortages hit, having a balanced inventory and access to quality sourcing keeps your production lines up and running — even during the height of a shortage market.
To summarize: Continuous market shortages on the horizon call for a fresh look at your shortage mitigation plan. Strategies including long-term materials management and capital planning can help.
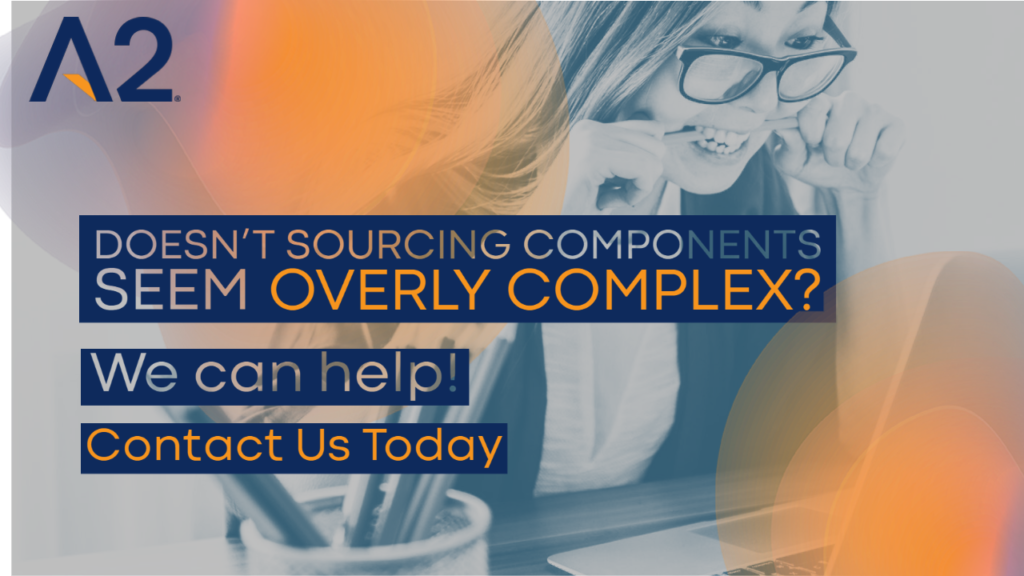
了解更多