In defense and aerospace, OEMs must strike a balance between the decades-long lifecycles of their products with internal electronic components that can become obsolete in less than five years. But just because your component may be approaching obsolescence, doesn’t mean your product needs to.
Boeing’s B-52 Stratofortress, referred to as “the backbone of the strategic bomber force for the United States” by the US Air Force, was first flown in 1954, and is expected to operate through 2050. On the other side of the spectrum, semiconductor leader NVIDIA releases a new GPU model every two years. With each new generation of electronic components comes inherently less support for older generations, and, eventually, a halt in production for older models.
OEMs that have done their due diligence have already identified which products will likely face obsolescence-related challenges by monitoring market developments, demand forecasting, supply chain shortages, and signs of end-of-life notices. Now what? Here are three strategies for mitigating legacy part obsolescence.
Find other suppliers and stock up.
The first and easiest step is to stock up on existing components and commit to a so-called “lifetime buy” to carry the product through its lifetime — or at least, for as long as possible.
In December 2022, the US Navy placed a $25 million order to Lockheed Martin Aeronautics to provide diminishing manufacturing source (DMS) management for its F-35 combat jets, specifically for electronic components such as computer processors, FPGAs, power supplies, and Databus Interface Chips. Lockheed’s solution: lifetime buys of the relevant electronic components.
While a quarter-billion dollar investment is far from pocket change, even for the US military, the purchase was described by John Keller, Editor-in-Chief of Military & Aerospace Electronics Magazine, as “a good deal” given the amount of time and money required to redesign and win certification for safety and performance of a new design.
Establish a solid network of suppliers and backup suppliers to source your electronic components. When stockpiling these essential parts, be sure to follow best practices for keeping your electronic safety stock safe. The only thing worse than being stuck without a backup supply of critical electronic components is having that supply compromised due to inadequate storage practices.
Identify alternative components.
The next step is to find alternative components that are different but can be integrated into your current system without a complete overhaul of the current design. This needs to happen at the initial design stage, with realistic program planning that accounts for all the details to make an accurate cost estimate of future upgrade needs.
In 2023, announcements of upgrades for the F-35 put the Department of Defense in the spotlight. Original estimates for the entire “Block 4 upgrade” for the F-35 were set at $10.6b with completion in 2026, but have risen to $16.5b with completion expected in 2029. “Fundamentally, the problem with the modernisation programme is that the DoD has not been able to distinguish its higher-than-expected costs, leaving the US Congress with ‘no clear picture of why demands and costs have spiked,’” as explained by Airforce Technology.
These rising costs led to an investigation performed by the US Government Accountability Office (GOA). In their report, they conclude that “the program did not complete an analysis of alternatives.” Additionally, the GOA found “analytical gaps in the program’s comparative analysis—in areas such as unaddressed technical risks and cost estimating—meaning that the military services’ decisions were not informed by this key information.”
When planning for alternative components, the GOA recommends the following for realistic cost estimations: take into account the purpose, scope, and schedule of a cost estimate; a technical baseline description; a work breakdown structure; ground rules and assumptions; data collection; estimating methodologies; sensitivity and risk analysis; documenting and presenting results; and updating estimates with actual costs.
McKinsey & Company recommends evaluating components by “fit, form, and function,” segmenting components by their risk of obsolescence and employing experts who can sufficiently assess the availability of alternative components.
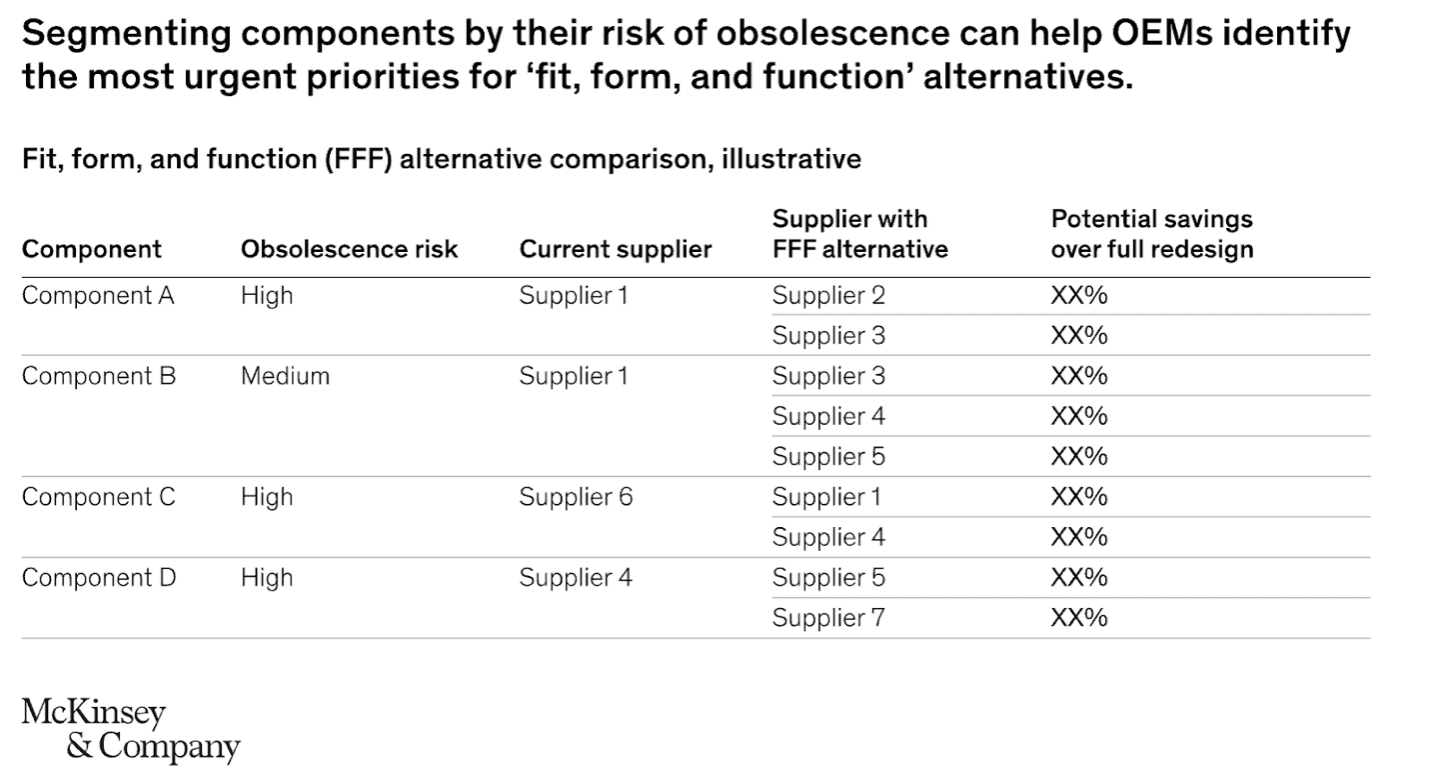
Source: McKinsey & Company
Develop redesign plans that carry your product into the future.
This is the step you want to avoid taking for as long as possible, while paradoxically being prepared for it as soon as possible.
The F-35 isn’t quite there yet, but making headlines like, “The world’s most sophisticated platform will be far less survivable than anticipated due to the US Government’s Block 4 mismanagement” doesn’t bode well. In the same announcement that revealed the contracts awarded for the F-35 upgrades, the complete redesigns of two other aircraft were also announced — one of which has only been used by the US Navy since 2018.
Assessing at what point in a product’s lifecycle a redesign will be necessary, along with its costs, can help OEMs extend the lifetime of their products and avoid costly redesigns before they’re absolutely necessary.
Proactive Obsolescence Management for Defense and Aerospace
Electronic component obsolescence is very different for aerospace and defense compared to other industries because the lifetimes of their products are significantly longer than the electronic components that support them. OEMs must take a proactive approach by identifying which of their components are at risk for obsolescence and devising a comprehensive long-term plan that outlines multiple suppliers, alternative components, and redesign plans.
Read more:
● End-of-Life Management: The Reactive VS. Proactive Approach
● 4 Storage Tips For Keeping Your Electronic Safety Stock Safe
● When Planning For Obsolescence, Stay Current To Stay Ahead