The semiconductor industry experiences relatively frequent boom and bust cycles. But impacts of this cycle have resonated more broadly in the past two years, with a confluence of factors impacting an already delicate balance of supply and demand.
With chip shortages likely to continue into 2024, some signs point to the semiconductor industry reaching more level ground now. Recovery, though, will be uneven and dependent on a number of factors including global economic outlook, geopolitical issues, and access to equipment to manufacture leading-edge chips.
One bright spot in the road to recovery is the passage of the CHIPS for America Act. This U.S. Act earmarks $52 billion for semiconductor research, design, and production in a bid to increase onshore manufacturing. On the whole, expanding capacity stateside would reduce shipping times and increase quality assurance.
The U.S. joins other countries around the world that have made similar commitments. Indeed, China, Taiwan, and India have undertaken efforts to onshore chip production. Although, because the semiconductor supply chain is highly complex, we will have to wait and see if these efforts can achieve stabilization of supply and demand.
Semiconductor shortage: How did we get here?
Even before the pandemic shutdowns in early 2020, semiconductor manufacturers were struggling to meet higher production targets. The situation was only exacerbated when Covid-19 shutdowns led to work-from-home consumers increasing their demand for electronics. At the same time, the electric vehicle (EV) marketplace saw unprecedented — and unpredicted — demand. In short, the market experienced unforecasted demand while supply dwindled.
Here, in one timeline, is an overview of recent events that have halted chip production and led to global supply constraints in the semiconductor space.
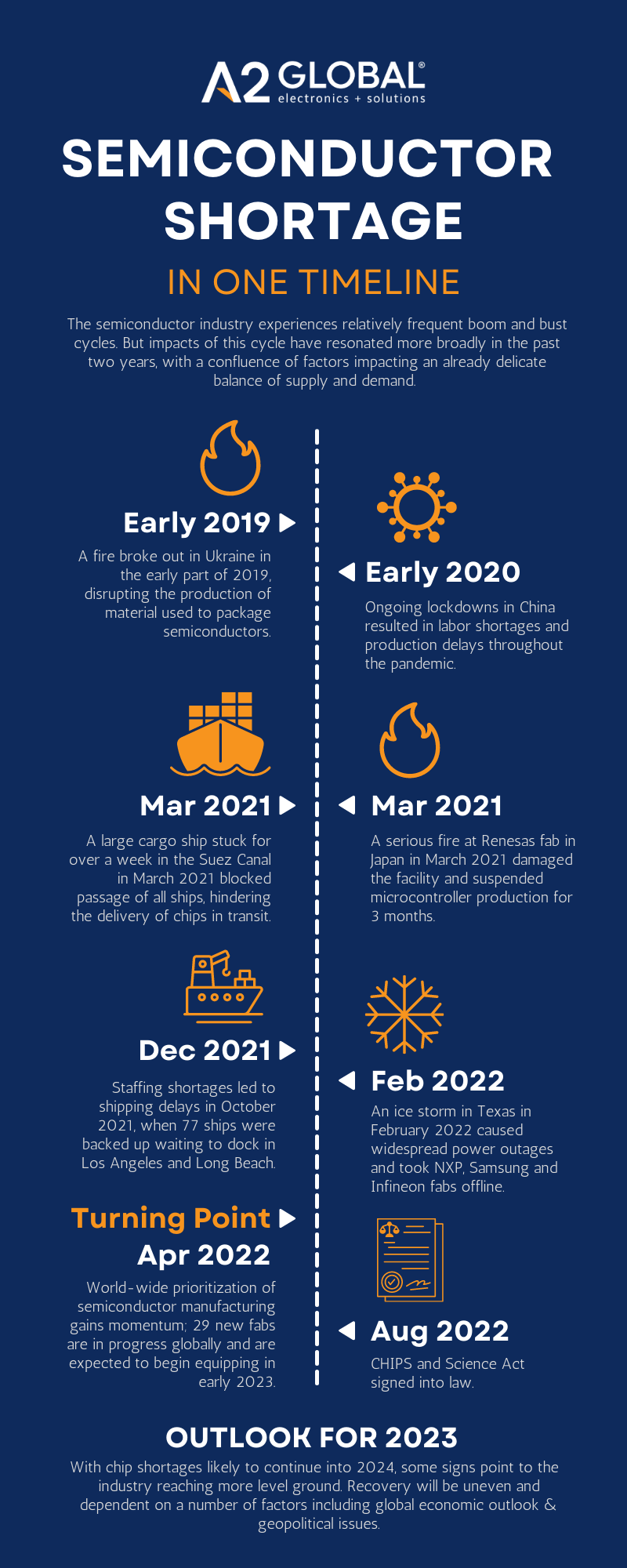
Manufacturers dilemma: Falling behind also means having to play catch up
Even without the constraints caused by the pandemic, these individual events — a cargo ship blocking a high-traffic shipping canal or an ice storm knocking out power to fabs in Texas, for example — would have no doubt contributed to some shortage of chips. And, when viewed through the lens of the pandemic, it becomes clear that any disruption in the supply chain can have far-reaching and long-lasting implications.
These shutdowns impacted global semiconductor manufacturers unevenly and for well beyond the time fabs were offline, as Tamera Max explains in Understanding the Current Global Semiconductor Shortage, Preparing for the Future:
The global shutdown affected semiconductor manufacturing companies across the world, unilaterally stopping wafer production. Fabs in some countries were offline longer than others and, depending on how the production line was paused, it took weeks to months to bring a fab back online. Once a fab is online, it takes 26 weeks to fill the production pipeline from wafer start to completion. Wafers are processed in lots or batches that take 12 weeks to cycle through the fab (14 to 20 weeks for complex process technologies). An additional 12 to 14 weeks are required for testing, die bonding and packaging. Manufacturers prioritized the existing semiconductor inventory to fill orders, so as fabs came back online, production was already lagging demand.
If chip shortages continue into next year as expected, you’ll want access to the most reliable, up-to-date stock availability and lead time averages. Working with an independent distributor that has relationships with manufacturers, electronic manufacturing service providers, and OEMs across the world gives you comprehensive, real-time insight into the market for semiconductors.
Read more: